From the title you may wonder 'Who is Max?' Well that's what I decided to name the little boy. Don't know why, but that's what I've named him :)
From my last post I explained that I was already creating molds for my character at the time of posting, well now I have finished my 2nd year of University and thought I have to update my blog! (I found it difficult to make time to update my blog through the chaos of major project, but here I go now!)
To start, the armature sheet.

These are the plans I followed while making the boy, and this will be the first time for me to use ball and socket joints for an armature. I was luckily enough to be given a 'INDY Range - H3 Solid Limbed Human Armature' by my university which was supplied by Malvern Armatures! The benefits of using ball and sockets over wire for those who may not know is that, unlike wire, the joints won't break and can be tensioned exactly how you want, even when the puppet is finished. The armature was given to be ready made and looked like this!
Therefore some disassembly and alterations had to be made to the armature which involved mixing past technique with the ball and sockets!
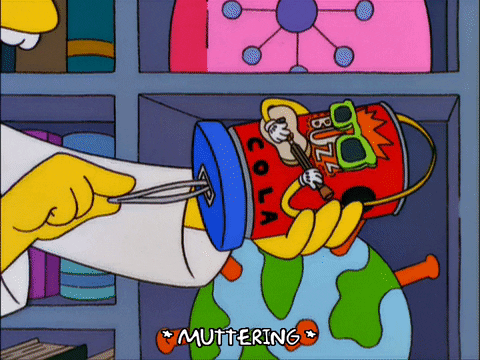
My first thought was making the legs shorter therefore I decided to only have the ball joint in the knee and replace the joint in the hip with wire. This would allow me to shorten the leg a lot more! With that in mind I bought a new, smaller 'double ball end' from malvern armatures which would replace the shin I already had.
Here's the Malvern armature website if you want to check that out!
http://www.malvern-armatures.co.uk/

Although the bar doesn't seem that much shorter, it makes a big difference within the armature!

I then began cutting K+S brass square tubing to length with a razor saw. The reason why I use K+S (if i haven't mentioned previously in my blog) is that smaller pieces of K+S can slot in to larger pieces of K+S. With this, wired joints can be epoxied within K+S and then slotted in to larger pieces of K+S which are acting as the hips and chest pieces.
When cutting the K+S to size the edges can become sharp and rough, this is not good!
1. Because it can restrict the K+S pieces slotting in to each other
and also
2. If the wire were to be put into a rough and jagged edged piece of K+S, as you bend a pose the wired skeleton, the rough edge can wear down and decrease the life span of the wire, causing the wire to break a lot quicker during animating!!
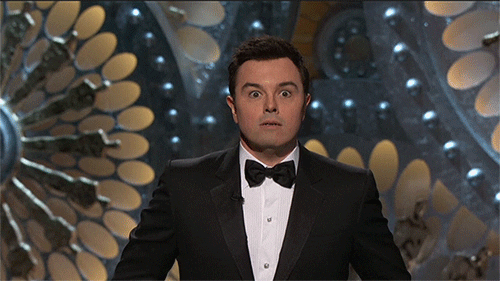
And we don't want that!!
So to prevent this and increase the life span of the wire, all edges of the K+S Pieces are filled down to ensure they are relatively smoothed and also heat shrink is also put on to the wire to give it a 'shell' which will again help prolong the life of the wire! Nice!
Here you'll see Max's arms finished.

With the image to the right you can see on your right that the K+S on Max's arm is all slotted together, with the arm to your left has been disassembled to show how they fit together.


To ensure the K+S pieces fit snuggly in to one another and to assure myself that and arm or leg wont slide out during filming notches are punched through lightly with a hammer and file.
This is a delicate task as you want to hit hard enough to create and indent, but at the same time light enough to ensure the 2 K+S Pieces are not locked together! My advice, practise on spare pieces of K+S first to gage the force needed for your preference.




For the hips my initial idea was to attach K+S pieces to a steel sheet, however due to the scale of the puppet being so small it was easier for me to adhere the K+S pieces together with some gorilla glue and then secure the pieces further with milliput later down the line :)
The same was also done to the chest piece.

The next thing that happened was something I thought that would happen...

Due to the rod being circular and smooth, after a few movements of the ball joint, the rod slid out from the dried epoxy. Im glad this happened while still constructing my armatures as this could prove a big problem if this happened during animating!

To fix this problem i began by using a razor saw ( a hacksaw would work to) and cutting little notches in to the rod to give the epoxy something to grip and set to.


I also sanded down the top of the rod in to a square, this was to ensure when the epoxy had set around it, the rod could not easily be moved or twisted.
Armature now coming together :) ....


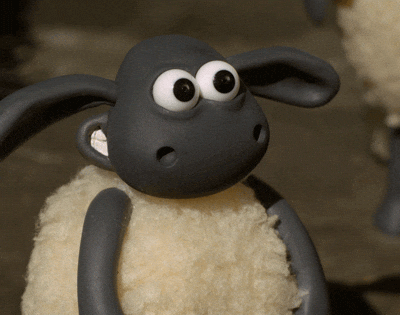
You might think that I'm jumping a few steps here as I go on to start sculpting , but this was an important step i needed to do to see if the thoughts in my head were correct...


Before sculpting I wrapped the ball joint with PTFE tape, this is not important until coming to cast however when it comes to removing the plastiline from the ball joint it makes it a lot easier and also stops plastiline getting in to the ball joint.


My assumptions were right, I thought the armature feet were to big for the scale of the boy. I added plasticine to see how much bigger the feet were going to be once bulked out and when seeing the sculpted I knew I wanted them a lot smaller.
Therefore it was time to think of a solution.
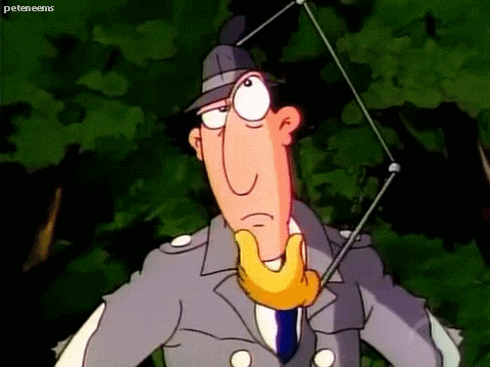
(If you look at the armature sheet you'll see what my plans were, but in the next post I'll show how I got there)
No comments:
Post a Comment