So yeah you may see from the title it says part 1, thats because the head and body have been hard work to do! Mainly the head, but you'll soon find out the problems I've had.
But you know what they say, mistakes are good!
So stay positive! Even if you're going mad inside!
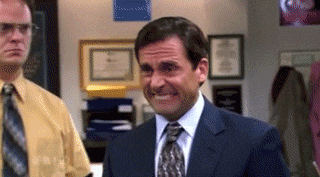
Lets start with the head!
As you know, I have made a balsa inner core to keep the head light, if not, 'bulking out' page here:
http://thomasvaughananimation.blogspot.co.uk/2016/01/bulking-out-body.html
so with that, I started covering the head with Premo clay, this was my first time using this, and I decided to use it as it comes in a variety of colours, plus it can be baked and hardened in the oven!
A mixture of different colours were used to achieve the colour I wanted.
After getting relatively bored mixing more and more pieces of premo I started to drift off subject and ended up with a pretty cool camouflaged slug!
Just thought I'd share that photo with you!
I then got back on topic and started mixing again.
This was the final result. The colour kept whilst baking, which was good. I would now have to mix the same colour green to place on the head for an eyebrow, to enable me to animate it.
But yeah, the head was sculpted, it was green, that was that, finished........
Is what I wished had happened


But yeah, the head was sculpted, it was green, that was that, finished........
Is what I wished had happened


As you can see from the images of the head above there are cracks and dents, and the whole thing is very uneven, which got me rather annoyed as this is not the standard I wanted in my work...
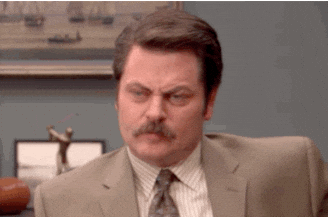
Therefore I knew I now needed to find a way of improving the head to a standard I wanted!
But before that I decided to move on to the shape of the body, as I now have a rough scale of the head.
Beginning the Body!!


I began by wrapping the balsa in cling film (saran wrap, if your not from the UK), this was to make things easier for me in the long run.
As after sculpting the bodyand making a mould, the clay would then need to removed from the inner core. Applying cling film to the balsa will enable me to remove the clay quickly and cleanly without damaging the sculpt.

Once wrapped, sculpey firm was added to the core.
But before that I decided to move on to the shape of the body, as I now have a rough scale of the head.
Beginning the Body!!


I began by wrapping the balsa in cling film (saran wrap, if your not from the UK), this was to make things easier for me in the long run.
As after sculpting the bodyand making a mould, the clay would then need to removed from the inner core. Applying cling film to the balsa will enable me to remove the clay quickly and cleanly without damaging the sculpt.

Once wrapped, sculpey firm was added to the core.

Clay kept being added to the balsa, and then the head was placed on top. I then took a loop tool and began shaving away any excess sculpey, and started defining the shape.

After shaving the sculpey I was left with a rough shape of Blob's body.

And from the shreds of his body grew some nicely shaped eyes.
That's enough for the time being, more on head and body next time!