Collaboration Project
The Animotion awards are the annual awards show for students of the Universtiy of South Wales. The show showcases students work from all three years which are part of the BA Animation (stop motion and 2D) class and the BA Computer Animation class. The theme each year changes. And this year, it was Sci- Fi!
Usually Martin, the stop motion tutor, would sculpt and cast the awards for the show. However this year Martin was unable to do it. With no one able to make the awards on such short notice. It was then asked for myself and Paul to create the awards for this years show.
After discussing the design and build with our lecturer and receiving great advice from Martin, we then began the process of creating the awards!
Paul has also documented his process of this project
pauljenkinsanimation.blogspot.co.uk
For the design of the trophy we were asked to create a UFO to match the Animotion 2016 logo. However the design of the UFO was completely up to us.
We had 9 trophies to make and a deadline of 1 week!
Heres the start to that very busy week!
After discussing the design and build with our lecturer and receiving great advice from Martin, we then began the process of creating the awards!
Paul has also documented his process of this project
pauljenkinsanimation.blogspot.co.uk
For the design of the trophy we were asked to create a UFO to match the Animotion 2016 logo. However the design of the UFO was completely up to us.
We had 9 trophies to make and a deadline of 1 week!
Heres the start to that very busy week!
To begin, Paul and I decided to split the award sculpt process in half to save as much time as possible. Therefore the ray/beam of the UFO was sculpted by Paul and the UFO itself was sculpted by me.
I started with blocking out a quick shape from SuperSculpey Firm.
I started with blocking out a quick shape from SuperSculpey Firm.
Once I was happy with the shape I started smoothing it out. To do this I wrapped the UFO in cling film and rolled a spray can over the sculpey. Once smooth I then unwrapped the UFO and applied lighter fluid to the sculpey to give a smoother finish.
The next step was to add the dome on top of the UFO and repeat the process of roughing out the shape, then smoothing. I used a lid to an olive oil spray bottle to smooth around the dome as it was convenient to use.
Once the sculpt was smooth, I could then place it in the oven to harde. I then sanded the sculpt down to get an even smoother finish.
The sculpted trophy will be moulded in a silicone mould therefore baking it hard will make it easier to remove it from the silicone.
And this was the end result! Now time to add a little detail.
I added milliput around the globe of the ufo to cover up the seam line and also added 4 half globes to the bottom of the UFO.
As you see Paul had finished the ray and it started to take shape!
to get the ufo to stay on top of the ray, we applied epoxy to the 2 sculpts.
This only had to stay secured until we had the silicone mould.

To tidy up the seam of the ufo and ray. Paul used miliput to sculpt some detail around the seam. This also gave more stability to the ufo and ray, insuring they don't come away from each other during moulding.
We wanted antennae to come out of each award, however this could not be apart of the ufo at this stage as we knew the antennae would break if they were attached to the ufo while moulding and casting.
Therefore we decided to drill 2 small indents in the top of the ufo. These indents were to give us registration points to ensure we could insert the antennae in to the same position on each trophy every time once all trophies were cast.
Therefore we decided to drill 2 small indents in the top of the ufo. These indents were to give us registration points to ensure we could insert the antennae in to the same position on each trophy every time once all trophies were cast.

Mould Making
To start the mould making process we hot glued a runner (in this case a rounded brass tube) to the bottom of the UFO and the base (corrugated plastic). We figured this section of the ufo would be a high point where air bubbles would collect when we started casting. Therefore to try and prevent this a runner is used to allow air bubbles to escape in to.Another problem which we could face is air bubbles in the silicone. Ideally when creating a silicone mould, a de-gassing chamber would be used to remove most of the air bubbles trapped in the silicone when mixing. As we do not have a de-gassing chamber we painted a layer of silicon on to the sculpt first. This would act as a barrier against air bubbles as well as making sure all detail of the sculpt would be picked up during moulding.
We then started boxing up the sculpt with foam board. The 2 pencil marks on the foam board was to allow us to see how far above the sculpt the silicone had to be. The bottom line was inline with the highest point of the UFO and the line above that is where we wanted the silicone to be filled to.

The mould required a LOT of silicone! As we did not have a big enough mixing stick to ensure the catalyst and silicone would be completely mixed in one tub. We decided to use 3 - 4 small tubs to mix the silicone. Paul was pouring the silicone in to the boxed sculpt as I was mixing the silicone.
The weight of the silicone began to push the foam board outwards so we began packing heavy objects up agains the box!
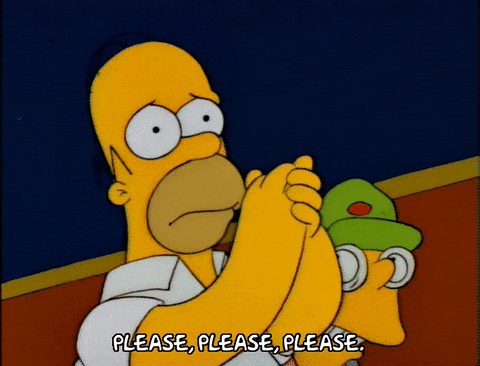
Hallelujah!! It worked!!
This is the mould after we had removed the sculpt from the inside. To remove the sculpt we cut in to one side of the mould. We cut halfway in to the silicone with a zig zag pattern, and as we got closer to the sculpt we cut a straight line. This was to ensure the seam line agains the trophy was straight but the zig zag would act as registration keys when the mould was closed to stop it from shifting.
You can see the outside of the silicone is cut as a zig zag and then the inner silicone is a straight line.


Casting
The trophies were cast in fast cast resin, using equal parts of Part A and B in the process. To limit the amount of fast cast used, yet reaching the needed amount of volume for each cast, we used a powder called 'Fordacal'. This powder can be added at any percentage to the Part A + B mixture to increase the volume.
Although by doing this it results in a heavier cast, but we liked the added weight to the trophies :)
With the ratios all calculated we began casting the trophies.
To keep the mould together we tried clamps but this caused the silicone to misshape. Therefore string was wrapped around the mould. The blocks on the side was to put equal amounts of pressure to the sides of the silicone.
Due to the fast cast heating up while curing it become to have an affect on the silicone. As we were casting more and more trophies one after the other, the mould became harder to close and realign properly causing the seam line to become less neat with each cast.
We now had all 9 cast!!
you may notice there's and extra one in the centre of the table. This had many air bubbles in it therefore we used this as a tester for our antennae and painting.

To create the antennae 2 moulds were made. One had a straight antenna and the other a crooked antenna. We decided to have one crooked to give more character to the ufo.
The straight antenna was simple to make. This was just a piece of rounded K+S with a ball of milliput on top. The crooked antenna was a bit more complicated. Three pieces of K+S were cut out and then glued back together in a crooked pattern. The corners were then neatened with milliput and a milliput ball was placed on top.
All three of the moulds we made can be seen above.
As Uni was closing, and a lot more needed to be done to the awards, we took them back to our student accommodation to keep working!
Holes were drilled in to the tops of the UFO to enable the antennae to slot in.
We used the tester cast to determine how far the antennae should go in and then marked them all with a sharpie. This was to ensure each award stayed consistent.
The antennae were then secured in to the holes with epoxy glue.
Casting all done on to Painting!!
Painting and Finishing
We were now very close to finishing. Only the painting and detail to do!
We used a grey primer to coat the trophies.

Once that was done it was on to the detail!
We thought it would be good to have a velvet base to the awards to ensure they did not scratch surfaces. We then thought it would be nice to include the animotion logo on the base in the centre of the velvet.
These were printed off on gloss paper and then laminated to ensure they would not get damaged while being at the bottom of the award. This process was done by my mother as I did not have a laminator on hand, so thank you to her for printing and laminating them :)
While I was making the base, Paul was painting the awards. We wanted an aged stone appearance to the awards. To keep a consistency in the appearance, Paul offered to paint each award as he had already used the painting technique in a recent project, while I did the velvet bases for each trophy.

Once the award had been painted, a coat of Crystal Clear - Matt finish was applied to the award, to ensure the paint was protected.
The Finished Awards
All in all, it was a very fun and exhausting, fast paced week. A lot of new techniques were used for the first time in the making of this, so I'm glad the trophies ended up looking this good!
Big thank you to Paul for his help, again his blog is at pauljenkinsanimation.blogspot.co.uk
Congratulations to all the winners and I hope you like your trophy!
Big thank you to Paul for his help, again his blog is at pauljenkinsanimation.blogspot.co.uk
Congratulations to all the winners and I hope you like your trophy!